In the pharmaceutical sector, drug traceability is crucial to ensure patient safety, comply with international regulations and prevent risks associated with counterfeit or spoiled products. Despite its importance, many companies face recurring problems when managing the traceability of their products.
This blog analyses the most common errors in drug traceability and proposes practical solutions to avoid them, helping companies improve their operational efficiency and ensure regulatory compliance.

What is drug traceability?
Drug traceability refers to the process of tracking a drug throughout its entire supply chain, from its manufacture to its final dispensing to the patient. This tracking includes key information such as:
- Place and date of manufacture.
- Product batch.
- Storage and distribution details.
Proper traceability ensures that the medicine is authentic, meets quality standards and is in optimal condition for consumption. It is also essential to prevent counterfeit medicines from entering the market.
For more information on the risks of untraceable medicines, the World Health Organization offers essential guides and resources.
The most common errors in drug traceability
1. Lack of technological integration
One of the most common mistakes is relying on manual methods or outdated systems to manage traceability. This can lead to:
- Loss of information.
- Failures in synchronization between process stages.
- Delays in identifying supply chain issues.
Solution
- Adopt technological tools such as specialized traceability software.
- Integrate digital systems, such as QR codes or blockchain, that allow automated and secure tracking.
- Train the team to efficiently manage these tools.
2. Incorrect or insufficient labeling
Labeling is key for traceability, but it is common to find:
-
- Poorly printed or illegible information.
- Codes that do not comply with international standards.
- Labels without sufficient data to ensure tracking.
.
Solution
- Implement advanced label printing systems that guarantee quality and legibility.
- Use barcode, QR or RFID labels to facilitate scanning and digital integration.
- Conduct periodic checks on the labeling process to avoid errors.
3. Lack of knowledge or non-compliance with regulations
Traceability regulations vary by country or region, and ignorance of these can lead to:
- Legal and economic sanctions.
- Loss of confidence on the part of consumers and distributors.
- Problems in the export or import of medicines.
Solution
- Stay up to date with local and international regulations, such as EU Delegated Regulation 2016/161 or the US DSCSA.
- Consult experts, such as PDG Consultant, specialized in pharmaceutical regulations and business management.
4. Improper inventory management
Poorly managed inventory can cause:
- Overstock and expiration of medicines.
- Economic losses due to unusable products.
- Delays in distribution due to shortages.
Solution
- Implement real-time inventory management systems.
- Apply the FEFO (first-expired, first-out) method to prioritize the release of products with closer expiration dates.
- Conduct regular inventory audits to detect and correct problems.
5. Lack of staff training
Staff who do not understand the importance of traceability can make mistakes that compromise the entire system, such as:
- Incomplete or incorrect records.
- Poor handling of technological tools.
- Lack of knowledge of emergency protocols.
Solution
- Design ongoing training programs on traceability, regulations and use of specific technologies.
- Establish clear and accessible protocols for the entire team.
Consequences of poor traceability
Inadequate traceability management can have serious effects on both public health and the company. The most common consequences include:
- Risks for patients: Lack of traceability can allow counterfeit or expired medicines to circulate, putting the lives of consumers at risk.
- Legal issues: Businesses that fail to comply with regulations may face fines, temporary closures or even loss of licenses.
- Economic impact: Poor inventory management and legal penalties can cause significant economic losses.
Benefits of optimizing traceability
By avoiding the above mistakes and adopting good practices, pharmaceutical companies can achieve:
- Greater operational efficiency: Error reduction and process optimization.
- Regulatory compliance: Avoiding sanctions and facilitating expansion into international markets.
- Consumer Confidence: Ensuring the quality and safety of medicines.
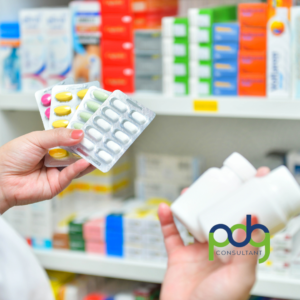
To ensure the traceability of medicines, Serialization is an essential toolThis process allows each product to be identified and tracked individually, which is key to complying with regulations and ensuring patient safety.
Pharmaceutical Serialization FAQs
Is it mandatory to implement advanced technologies for traceability?
In many countries it is not mandatory, but the use of technologies such as blockchain, ERP or RFID tags significantly improves accuracy and regulatory compliance.
What to do if a counterfeit medicine is detected in the supply chain?
It must be withdrawn immediately and the competent authorities notified. Having an efficient traceability system facilitates this action.
What is the most relevant regulation in Europe for traceability?
Delegated Regulation 2016/161 establishes clear guidelines on the use of unique identifiers and verification systems in the European Union.